Specialist Engineering
Process Group offers an extensive range of specialist engineering services that complements and supports our core process engineering service. From functional safety engineering and petrochemical plant design through to specialist expertise for rotating equipment design, procurement and commissioning.
Expertise is offered across hydrocarbon, hydrogen, syngas, ammonia and urea plant production technologies. We promote best practice with applicable codes, standards and legislative requirements, utilising best-in-industry tools and technologies.
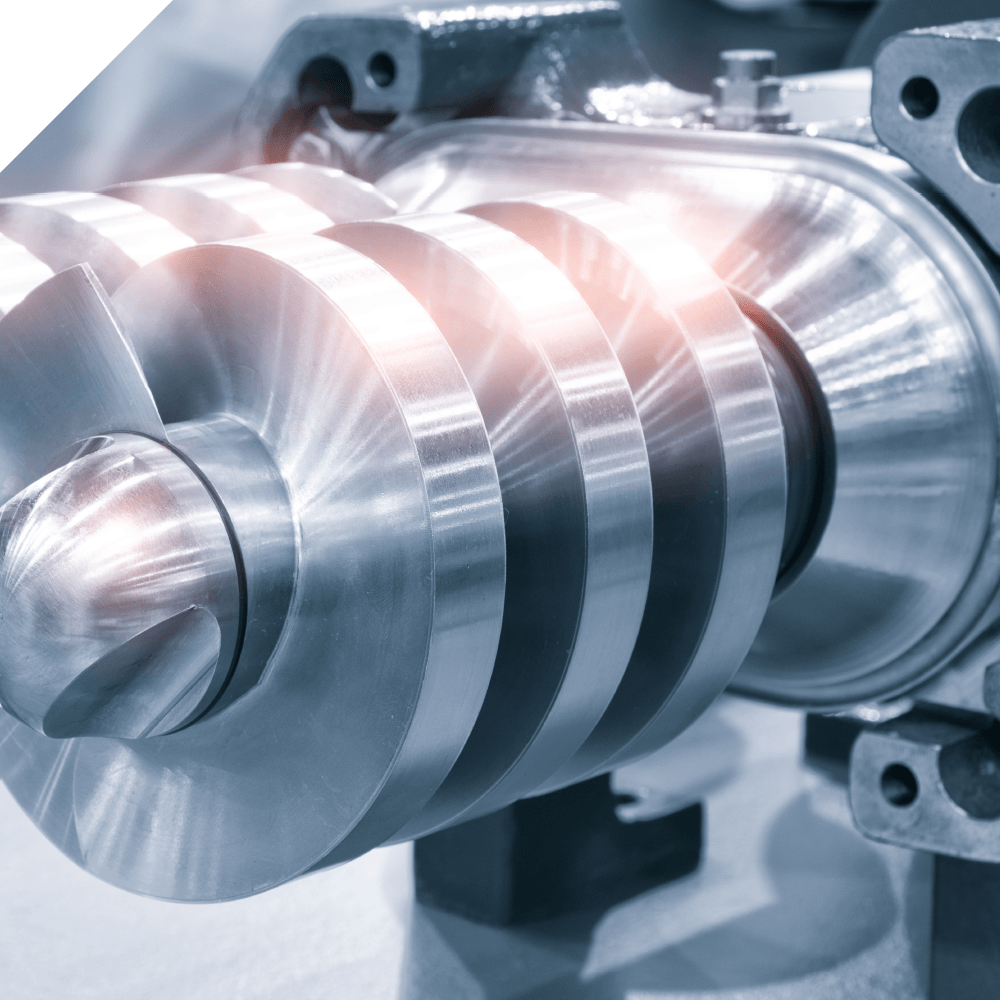
Specialist expertise for
your project
FUNCTIONAL SAFETY ENGINEERING
Process safety instrumented systems (SIS) comprise many individual safety instrumented functions (SIFs) designed to move a plant or process unit to a safe state when something goes wrong. These functions are active layers of protection and should happen automatically when an undesired condition arises. The IEC 61511 standard defines a functional safety lifecycle for these SIFs.
From concept through to de-commissioning, Process Group has specialist expertise in functional safety across the project lifecycle, providing services in accordance with IEC 61511 requirements.
- Functional Safety Management
- Develop/review functional safety management plans
- Perform functional safety audits, assessments, and verification
- Risk Reduction
- Support/review of HAZOP & LOPA studies
- Safety Requirements Specifications
- Safety Instrumented Systems (SIS) Design
- Design & engineering of safety instrumented systems and functions
- PFDavg calculations using fault tree and other methodologies
- Operational support for installation, commissioning and validation
ROTATING EQUIPMENT ENGINEERING
Rotating equipment is central to the successful operation of process plants, from gas compressors to power-generating turbines to product-transfer pumps. It is therefore critical that this equipment is properly specified, procured, and maintained.
We offer services for a range of rotating equipment including:
- Centrifugal, reciprocating and screw compressors
- Centrifugal and positive displacement pumps
- Multi-phase pumps
- Firewater pumpsets
- Gas turbines and engines
From assessing equipment feasibility during concept development, through to package engineering, site installation and commissioning of a wide range of rotating equipment, Process Group offers the full range of rotating equipment services.
- Concept Select
- Feasibility assessments, equipment recommendations and cost assessment
- Reliability and Maintenance impacts and improvements
- Package Engineering
- Specifications and datasheets
- Technical prequalification and Technical Bid Evaluation
- Third-party inspection monitoring
- Factory Acceptance Tests
- Documentation review and approval
- Installation and commissioning procedures
- Construction Support and Commissioning
- Storage and preservation procedures
- Grouting specification
- Pre-commissioning and commissioning procedures
- Operational Support and Troubleshooting
PETROCHEMICAL PLANT EXPERTISE
Process Group has significant petrochemical plant design and operating expertise established from over 30 years of involvement in the syngas industries. Ammonia-urea plant experience is particularly notable together with methanol and hydrogen peroxide plant major project experience. Working with international technology licensors for ammonia, urea and hydrogen peroxide plant design has also been a key feature over this time:
- Plant modifications
- Revamps
- Process simulation
- Equipment design
- Catalyst specification
- Plant optimisation
- Production and efficiency improvements
Tools and Capability
Process Group utilises the world's leading engineering software, to deliver unparalleled accuracy and certainty. Our highly experienced team has best-in-class process engineering capability in a number of areas including Process Simulations, Relief & Flare System Design, Consequence Modelling (PHAST), Heat Exchanger Design and Optimisation.
Isograph's integrated software products provide a powerful and comprehensive suite of tools to solve complex problems. This includes reliability and safety analysis, availability simulation and maintenance optimisation, security analysis and threat assessment, network availability prediction and hazard and operability studies.
Heat Transfer Research, Inc. is the global leader in process heat transfer and heat exchanger technology. Considered the industry’s most advanced thermal process design and simulation software, HTRI rates, simulates, and/or designs a variety of heat transfer equipment.